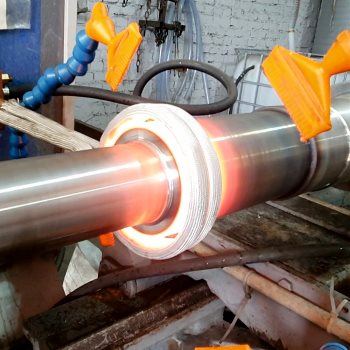
Загартування СВЧ (індукційне загартування)

Загартування СВЧ (індукційне загартування)
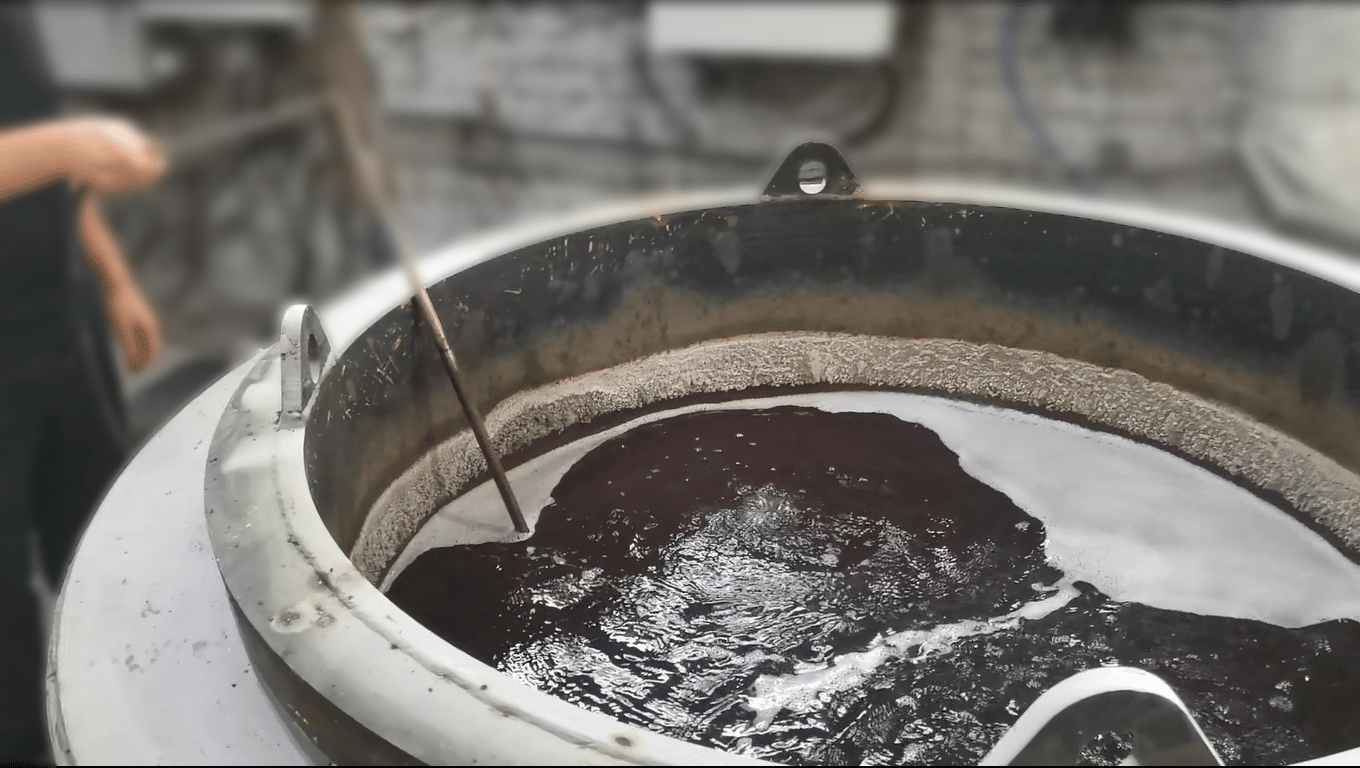
Нова піч для рідинного азотування
Піч для Рідинного Азотування – Новий Крок В Розвитку Нашого Підприємства
Суми, 26.10.23 – Наше підприємство завжди прагнуло до інновацій та вдосконалення процесів, і ми раді представити вам наше останнє досягнення – нову піч для рідинного азотування з вражаючими робочими габаритами.
Дана піч має розміри робочого простору Ø1150 х 700 мм, що відкриває перед нами нові можливості в галузі обробки великогабаритних деталей. Завдяки цій пічі ми можемо проводити рідинне азотування деталей діаметром до 1100 мм та висотою до 700 мм.
Така піч стала єдиною в Україні, що дозволяє проводити карбонітрацію настільки великих деталей, і це відкриває перед нами нові перспективи у співпраці з клієнтами.
Наша мета надавати найвищу якість послуг, і нова піч є ще одним кроком вперед у досягненні цієї мети. Ми раді можливості надавати нашим клієнтам ще більше варіантів обробки.
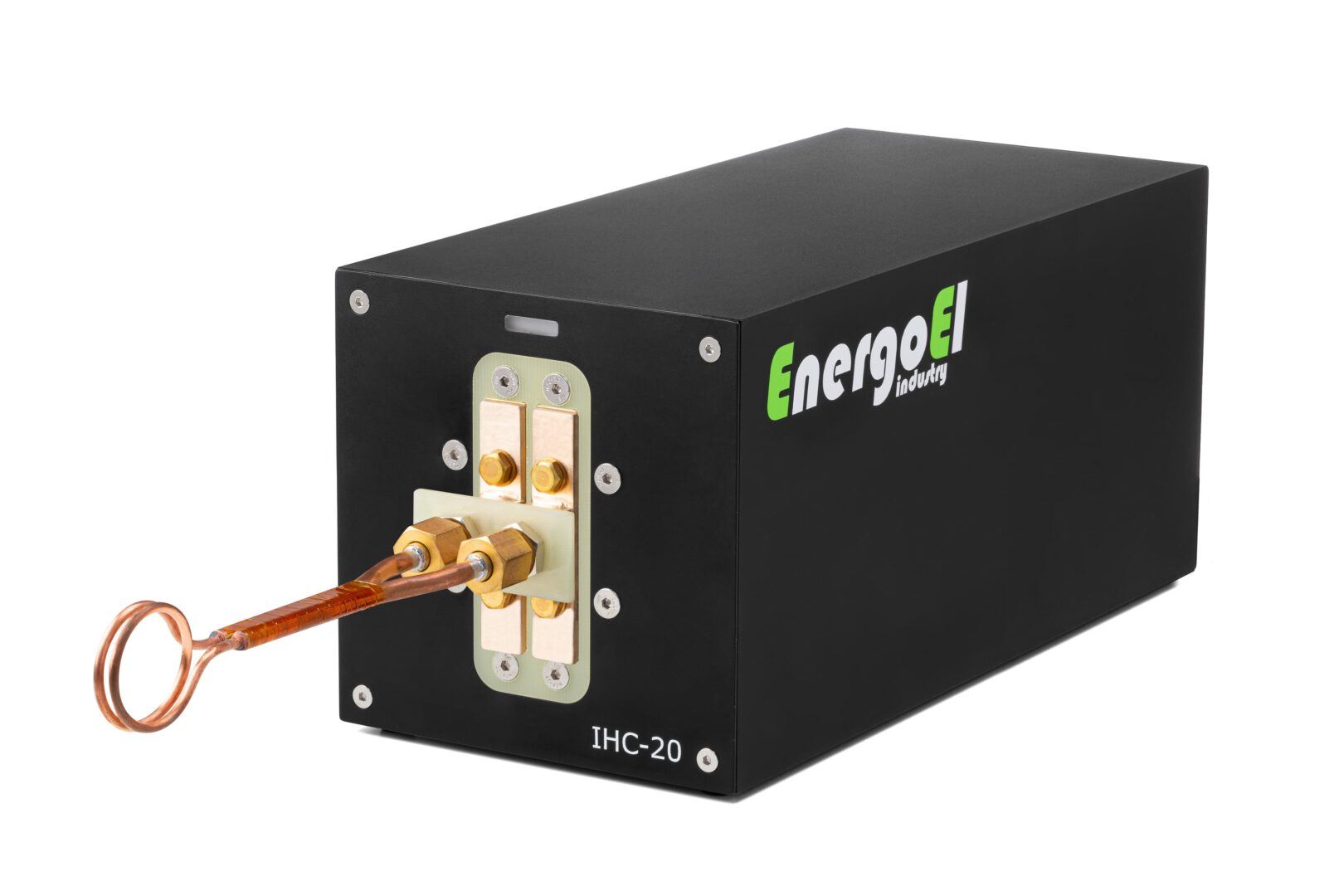
НОВА УСТАНОВКА ДЛЯ СВЧ ЗАГАРТУВАННЯ
НОВИЙ ЕТАП РОЗВИТКУ: НАША КОМПАНІЯ ВПРОВАДЖУЄ УНІКАЛЬНУ УСТАНОВКУ ДЛЯ СВЧ ЗАГАРТУВАННЯ
Суми, 26.10.23 – Наша компанія із задоволенням представляє новий етап у своєму розвитку – впровадження та освоєння EnergoEl IHC-15, компактної установки струму високої частоти (СВЧ), для індукційного загартування.
Індукційне загартування СВЧ є одним із найбільш економічних та технологічних методів зміцнення деталей машин. Ця методика дає можливість загартовувати поверхню деталей або її окремі елементи, які піддаються найбільшому завантаженню. В результаті цього процесу можна отримати тверду зовнішню поверхню деталі, залишаючи внутрішній шар м’яким та в’язким. Така структура дає високу стійкість, надійність та міцність виробів, що є ключовими характеристиками в сучасній промисловості.
Найважливішою особливістю СВЧ загартування є частота роботи. Завдяки підвищеній частоті струму досягається ефективна концентрація тепла на обмеженій площі, що призводить до високошвидкісного нагрівання до декількох сотень градусів за секунду. Наша нова установка використовує надвисокі частоти, що робить її унікальною в порівнянні з більшістю інших установок СВЧ в Україні. Це дозволяє більш точно регулювати глибину загартованого шару.
Більшість установок СВЧ, які поширені в країні, включаючи нашу першу, працюють з робочою частотою від 15 до 30 кГц. Це дозволило досягти глибини загартованого шару близько 2,5 мм. Однак нова установка, здатна працювати з частотами від 60 до 300 кГц, що надає можливість більш точного контролю глибини загартування, яка може становити менше 1 мм. Це дозволяє проводити термообробку окремих впадин та зубів шестерні з надвисокою точністю.
Окрім того, нова установка дозволяє робити термообробку малогабаритних, тонких деталей та складних виробів. Це дозволяє нам працювати над більш складними та інноваційними проектами.
Впровадження нової установки для загартування СВЧ є кроком у розвиток нашої компанії, розширює наш арсенал технологій та можливості надавати якісні послуги з термообробки.
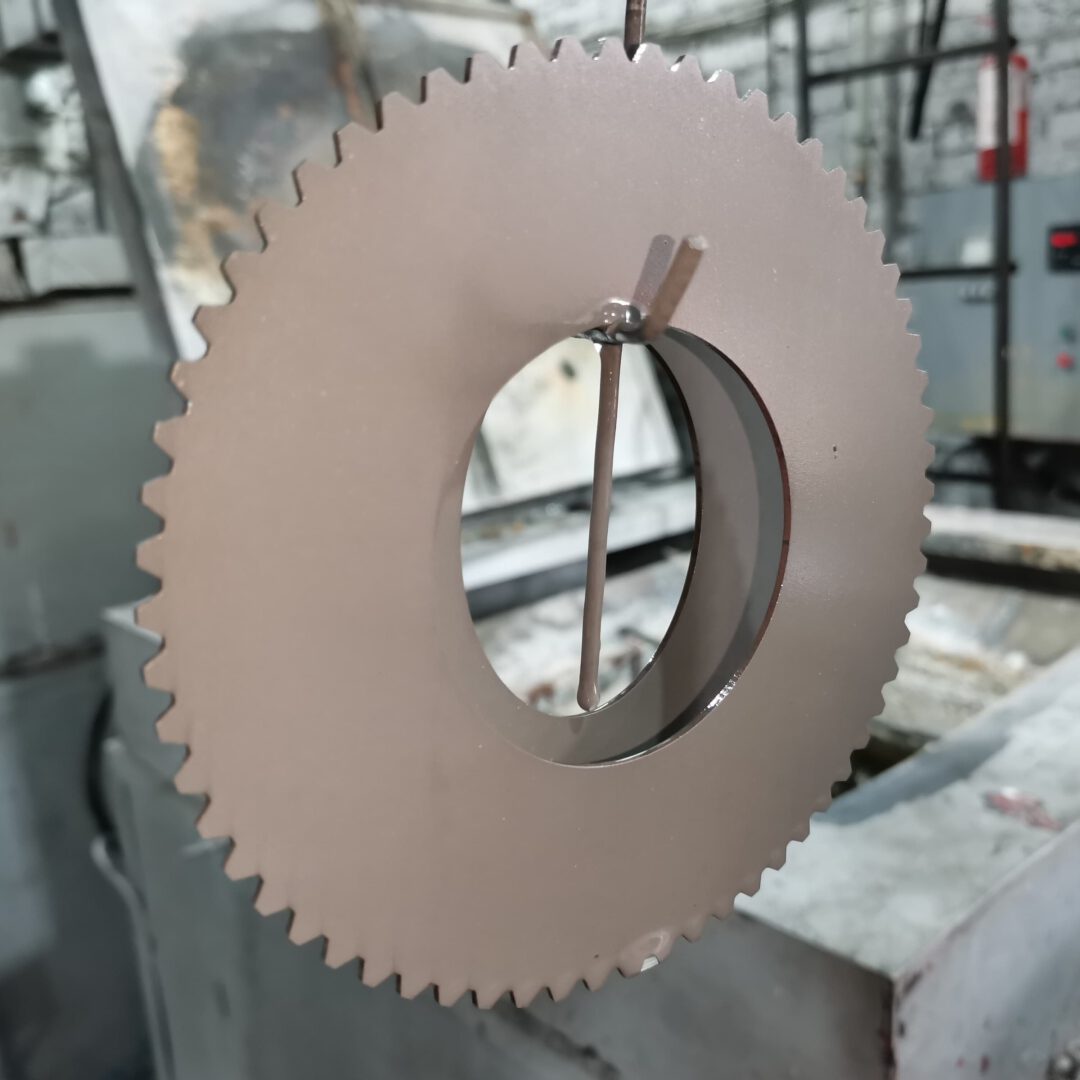
Сульфоціанування

Сульфоціанування

Наші технічні можливості щодо сульфоціанування

МЕТА СУЛЬФОЦІАНУВАННЯ

Основні етапи виготовлення деталей, що піддають сульфоціануванню
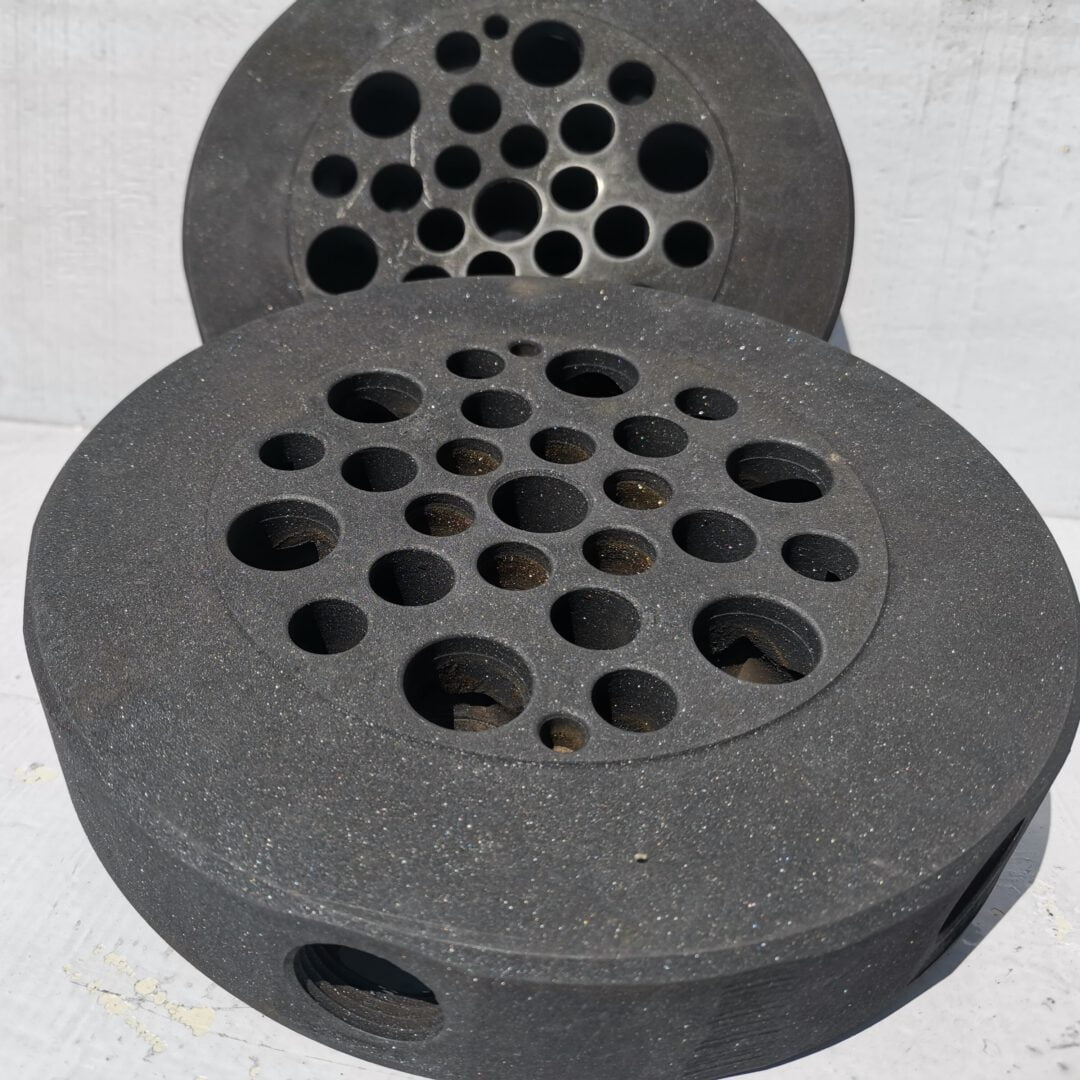
Борування

БОРУВАННЯ

НАШІ ТЕХНІЧНІ МОЖЛИВОСТІ ПО БОРУВАННЮ

ЦІЛЬ БОРУВАННЯ

Основні методи насення боридного покриття
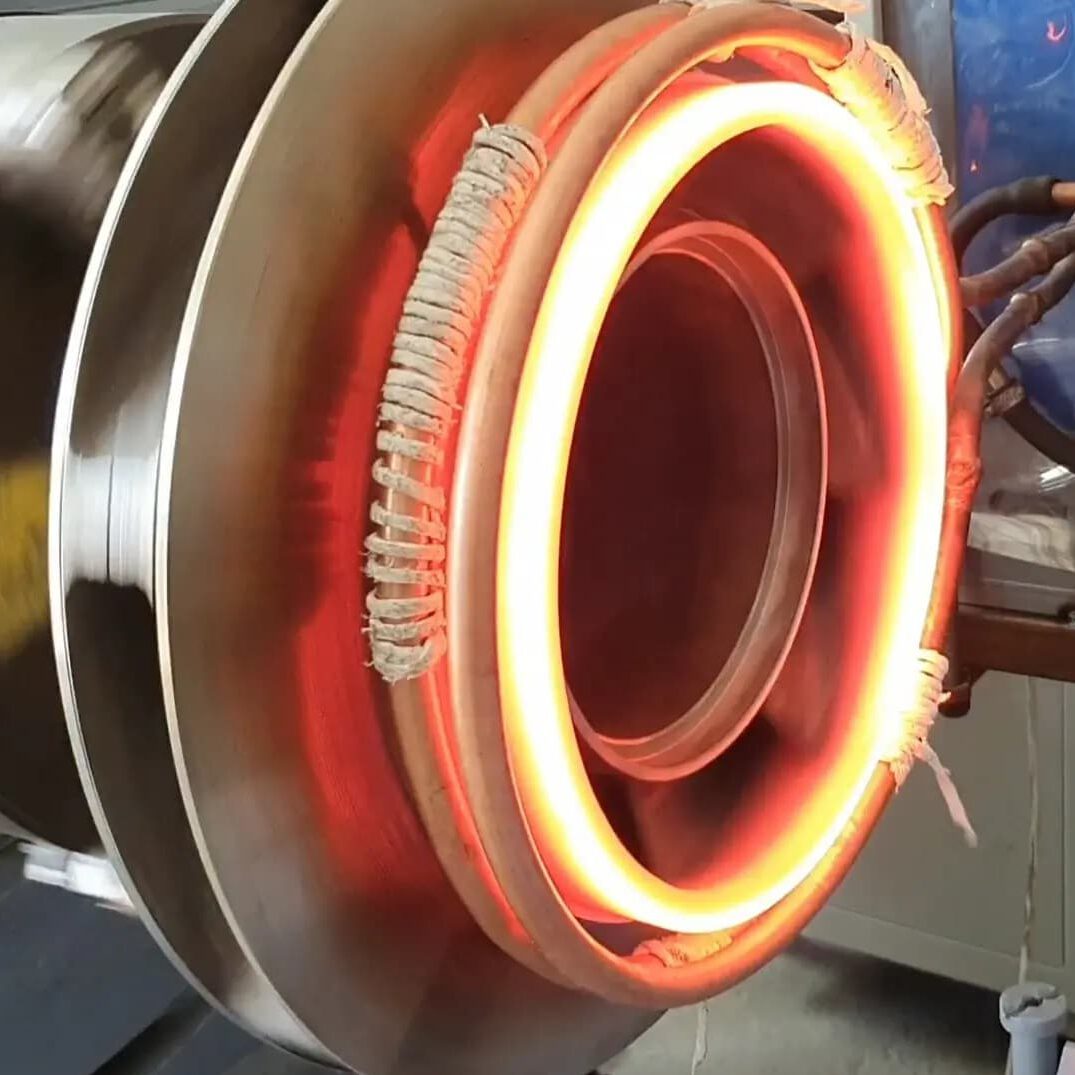
СВЧ

Загартування СВЧ

Наші технічні можливості по СВЧ

Принцип роботи СВЧ

Переваги СВЧ
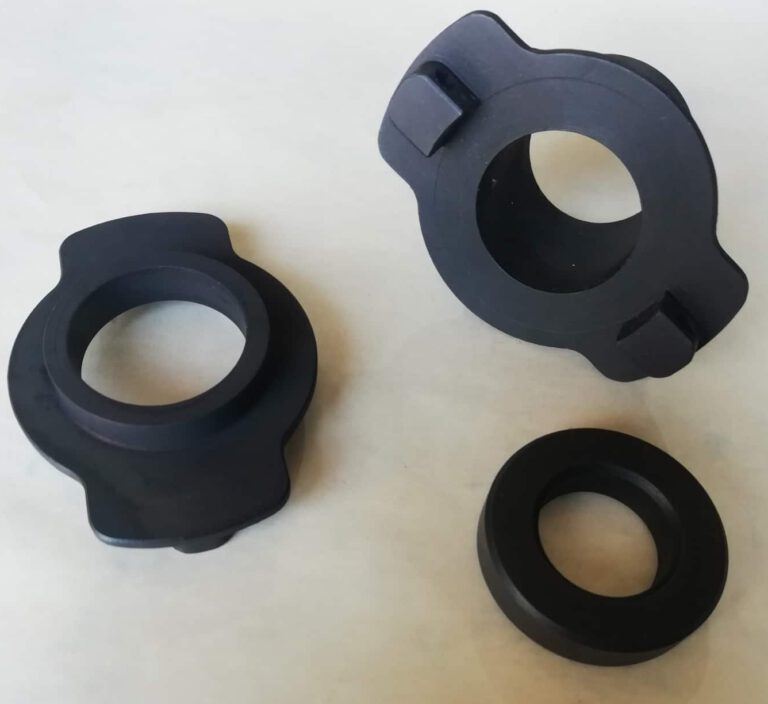
Фосфатування

Опис

Наші технічні можливості по фосфатуванню

МЕТА ФОСФАТУВАННЯ

Основні етапи виготовлення деталей, які фосфатують
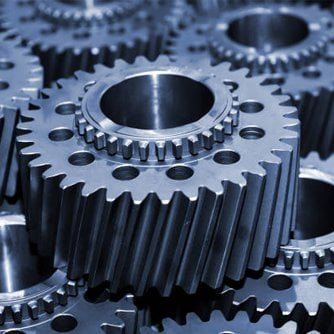
Сульфоціанування

Сульфоціанування

НАШІ ТЕХНІЧНІ МОЖЛИВОСТІ ПО СУЛЬФОЦІАНУВАННЮ

МЕТА СУЛЬФОЦІАНУВАННЯ

Основні етапи виготовлення деталей, що піддаються сульфоціануванню
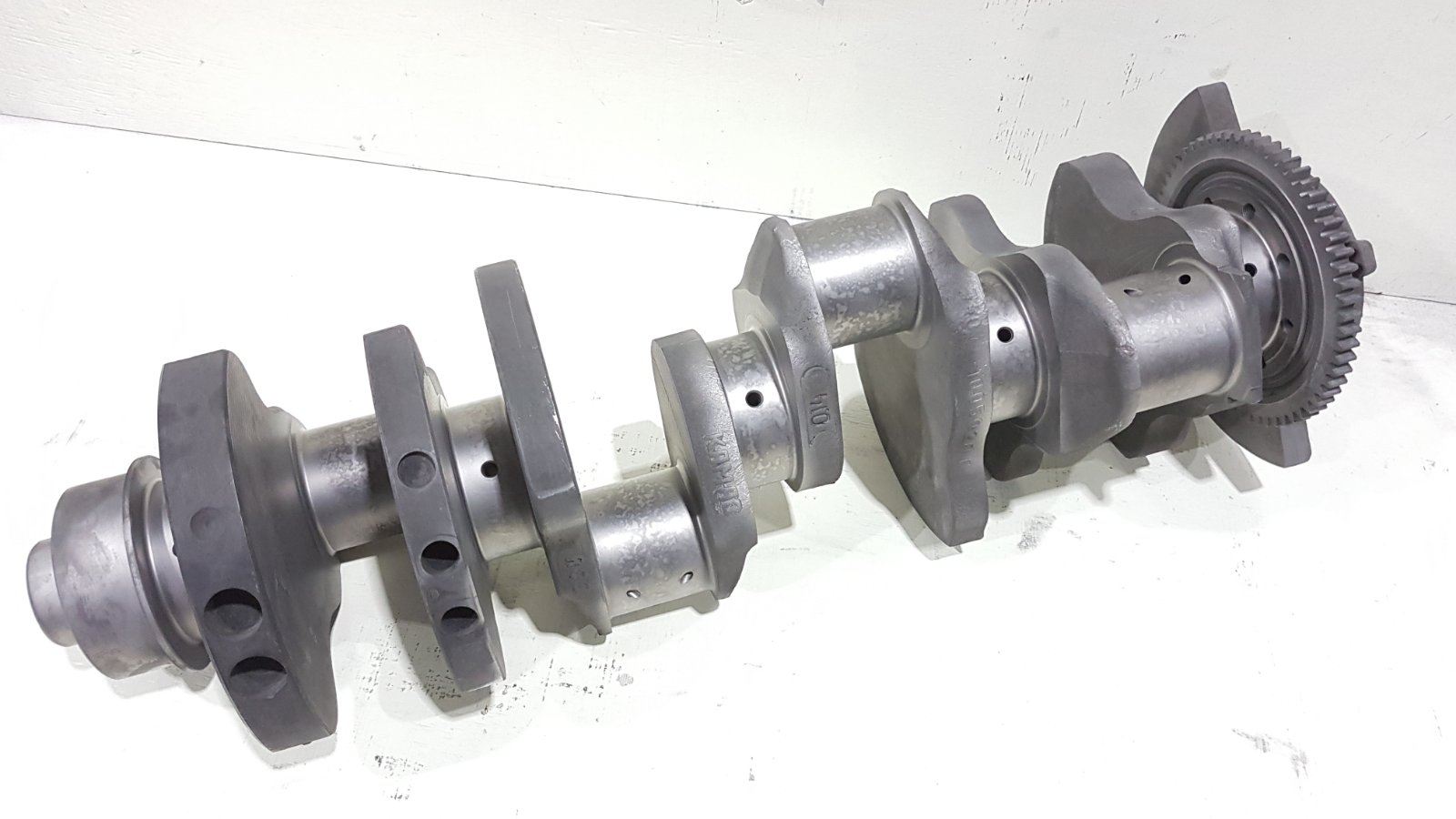
Зміцнення Колінчастого вала КАМАЗ
Колінчастий вал – один з найбільш відповідальних і дорогих конструктивних елементів двигуна внутрішнього згоряння. Ця деталь (або вузол деталей в разі складеного валу) складної форми, що має шийки для кріплення шатунів, від яких сприймає зусилля і перетворює їх в крутний момент. (більше…)