Термічна обробка

Опис
Термічна обробка – це послідовність операцій нагріву до заданої температури, витримці при цій температурі і охолодження із заданою швидкістю твердих металів і їх сплавів.
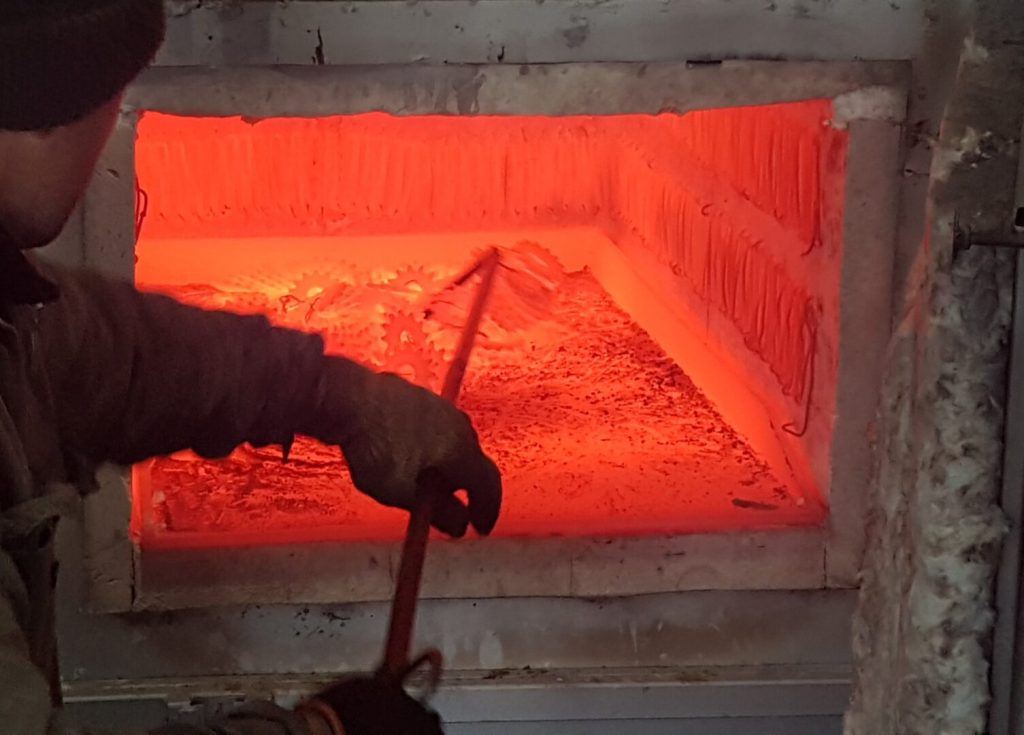
Мета термічної обробки – отримання необхідних механічних і фізичних властивостей (поліпшення оброблюваності, підвищення або зниження твердості і міцності стали і т.п.) металів і їх сплавів в результаті зміни внутрішньої будови і структури без зміни форми виробу і складу.
Термічна обробка може застосовуватися або як проміжна операція (попередня термообробка) для поліпшення оброблюваності тиском, різанням, зняття напруги і ін., Або як остаточна операція (остаточна термообробка) технологічного процесу, що забезпечує заданий рівень властивостей виробу.
Кваліфікований досвідчений персонал і устаткування, наявне у нас на підприємстві, дозволяють виконувати більшість відомих видів термічної обробки:
Наші технічні можливості
- Відпал, нормалізація, аустенізація, загартування на повітрі або в воді, відпуск, старіння – деталі діаметром до 900 мм, довжиною до 1250 мм, вагою до 2 тонн.
- Загартування в маслі і безмасляному загартувальному середовищі – деталі вагою до 100 кг
- Загартування в соляній печі-ванні – деталі діаметром до 400 мм, довжиною до 450 мм, вагою до 30 кг
- Загартування СВЧ – потужність установки 120кВт. Параметри оброблюваних деталей уточнюються в кожному конкретному випадку.
Наші технічні можливості
- Відпал, нормалізація, аустенізація, загартування на повітрі або в воді, відпуск, старіння – деталі діаметром до 900 мм, довжиною до 1250 мм, вагою до 2 тонн.
- Загартування в маслі і безмасляному загартувальному середовищі – деталі вагою до 100 кг
- Загартування в соляній печі-ванні – деталі діаметром до 400 мм, довжиною до 450 мм, вагою до 30 кг
- Загартування СВЧ – потужність установки 120кВт. Параметри оброблюваних деталей уточнюються в кожному конкретному випадку.
Компанія Карбаз пропонує послуги термічної обробки металу, що включають вороніння, відпал, нормалізацію та загартування сталі різних марок та розмірів. Ці процеси забезпечують зміну властивостей матеріалу, роблячи його більш міцним, твердим та довговічним.
Вороніння – це процес термічної обробки металу, який використовується для покращення його механічних властивостей. В результаті воронення метал набуває підвищеної міцності та твердості, що робить його ідеальним для використання в умовах підвищених навантажень.
Відпал – це процес термічної обробки металу, який використовується для зняття внутрішніх напруг, покращення пластичності та підвищення деформованості матеріалу. Відпал також допомагає усунути дефекти металу, покращуючи його якість.
Нормалізація – це процес термічної обробки металу, який застосовується для покращення його механічних властивостей та підвищення міцності. Нормалізація призводить до поліпшення структури металу та підвищення його твердості.
Загартування – це процес термічної обробки металу, який використовується для підвищення його твердості та міцності. При загартуванні метал швидко охолоджується у спеціальних середовищах, що призводить до перетворення його структури та формування мартенситу. Це робить метал більш міцним та твердим.
Компанія Карбаз пропонує якісну термічну обробку металу на сучасному обладнанні, що дозволяє отримати матеріали з оптимальними механічними властивостями. Наші фахівці мають багаторічний досвід роботи та готові надати нашим клієнтам послуги високої якості.
Виконуємо послуги по Гартуванню та нормалізація сталі 20, 40х, 45, відпалу металу, чавуну, міді, латуні, термічній обробці металів втулки, пружини, шестерні, валу від КАРБАЗ – Київ, Харків, Дніпро, Суми