Cyaniding of Metal and Steel

Description
Cyaniding is a type of chemical-thermal treatment that involves the diffusion saturation of the steel surface layer with nitrogen and carbon in molten cyanide salts. The goal of cyaniding is to increase hardness, wear resistance, bending endurance, and corrosion resistance.
Cyaniding of components is performed at temperatures ranging from 550 to 960°C in bath furnaces containing molten cyanide salts such as NaCN, KCN, and others mixed with neutral salts like NaCl, Na₂CO₃, CaCl₂, and others.
The main disadvantage of this chemical-thermal treatment process is the high toxicity of cyanide compounds and the associated environmental hazards of their use, which necessitates separate rooms and ventilation systems, as well as heightened safety measures for each bath. Additionally, the relatively high cost of the chemicals used for the saturating medium also impacts the economic aspect of the process.
Therefore, liquid cyaniding is currently not used in mass and serial production and is very limited in single-piece production.

CARBONITRATION AS AN ALTERNATIVE TO CYANIDATION
Cyaniding is, in terms of its purpose and effect on the surface layer of steel products, a 100% equivalent to the process of carbonitriding. However, carbonitriding is non-toxic, as it is performed in cyanide melts that are completely harmless to humans and easy to use.
Our company, Karbaz LLC, does not use the cyaniding process and instead offers our customers a more advanced and safer carbonitriding process.

CYANIZING PROCESS
Currently, cyaniding and nitrocarburizing are among the most sought-after services offered by our company, Karbaz.
The cyaniding process is a hardening technology involving chemical-thermal treatment with cyanide salt solutions at temperatures between 550°C and 960°C, resulting in the saturation of steel with carbon and nitrogen. This procedure enhances the metal’s endurance limit, hardness, wear resistance, and reduces its susceptibility to corrosion.
The concentration of nitrogen and carbon in the surface layer depends on the duration of cyaniding and the temperature settings. Higher temperatures result in a higher carbon content, while lower temperatures lead to a higher nitrogen percentage.
However, the cyaniding process is highly toxic and harmful to health and the environment. It is conducted in specialized baths that must be located in well-ventilated rooms.
Due to the high toxicity of cyaniding steel, it is now rarely used in mass production. We offer you to replace it with carbonitriding, which provides similar results but is completely environmentally safe.
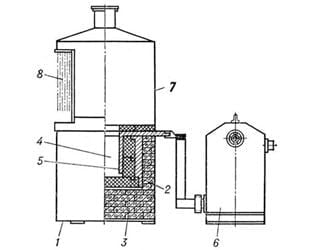
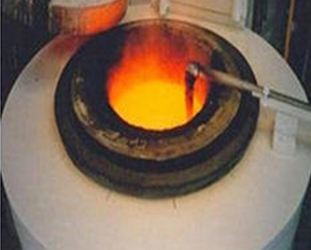
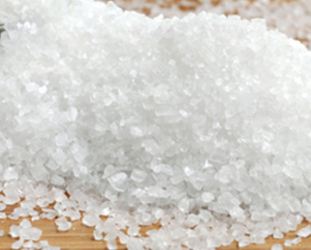
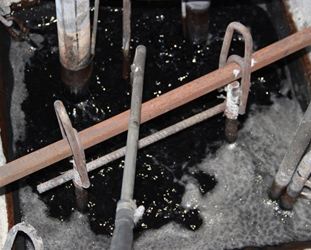

TYPES OF CYANIZING
Cyaniding is a type of chemical-thermal treatment involving the diffusion saturation of the steel’s surface layer with nitrogen and carbon in molten cyanide salts. The aim of cyaniding is to enhance hardness, wear resistance, bending endurance, and corrosion resistance.
Cyaniding is performed at temperatures ranging from 550°C to 960°C in specially equipped baths containing molten cyanide salts such as NaCN (sodium cyanide), KCN (potassium cyanide), and others, mixed with neutral salts like NaCl (sodium chloride), Na₂CO₃ (sodium carbonate), and CaCl₂ (calcium chloride).
Low-temperature cyaniding is carried out at 550–570°C in salt baths containing approximately 40% KCN and 60% NaCN, with dry air passing through. In this case, steel is predominantly saturated with nitrogen rather than carbon. This method is used to increase the hardness, wear resistance, and heat resistance of high-speed steel tools and medium-carbon steel parts. The process duration ranges from 0.5 to 6 hours. For high-speed tools, the layer depth is 0.015–0.04 mm, and for machine parts from construction steels, it is 0.1–0.5 mm. No additional thermal treatment is required after low-temperature cyaniding.
Medium-temperature cyaniding is conducted at 820–860°C in molten salts, typically a mixture of 40% NaCN, 40% NaCl, and 20% Na₂CO₃. The process lasts between 30 to 90 minutes. The depth of the layer is 0.15–0.35 mm. Parts are quenched directly from the cyanide bath and then tempered at 180–200°C. The hardness of the cyanided layer after thermal treatment is HRC 52–62. The cyanided layer contains 0.8–1.2% N and 0.6–0.7% C.
High-temperature cyaniding is carried out at 930–960°C in molten salts containing approximately 8% NaCN, 10% NaCl, and 82% BaCl₂ (barium chloride). The process lasts from 1.5 to 6 hours. The layer depth is 0.15–2.0 mm. Due to the high temperature and the resulting grain growth in the austenite, direct quenching is not performed. Parts are air-cooled and then subjected to quenching and low tempering. The hardness of the cyanided layer after thermal treatment is HRC 63–65. The layer contains 0.8–1.2% C and 0.2–0.3% N. Compared to cementation, high-temperature cyaniding has advantages such as shorter process duration, less deformation and warping of complex-shaped parts, and higher resistance to wear and corrosion.
Cyaniding steel is a surface hardening process that improves the mechanical properties of metal, providing greater strength and wear resistance.
Cyaniding is a method of metal hardening based on saturating the surface of the part with nitrogen, cyanides, and carbonates. This results in a layer of compounds containing carbon and nitrogen. Cyaniding is used to improve wear resistance, corrosion resistance, and increase the hardness of steel.
We, providing cyaniding services, have modern equipment and experienced specialists who ensure high-quality metal processing and compliance with customer requirements. You can order steel cyaniding services from us and obtain metal with enhanced mechanical properties and increased wear resistance.