Steel Cementation

Description
Cementation – a chemical-thermal treatment involving the diffusion of carbon atoms into the surface layer of steel products by heating to a temperature of 900-950 °C.

MICROSTRUCTURE OF THE CEMENTED LAYER
The cemented layer has a variable carbon concentration across its thickness, decreasing from the surface towards the core of the component. As a result, after slow cooling, the structure of the cemented layer can be differentiated into three zones:
Surface Zone (High Carbon Content): This is the outermost layer with the highest carbon concentration. It is characterized by a high hardness and wear resistance due to the presence of a significant amount of cementite and martensite. This zone provides the primary protection against wear and surface damage.
Transition Zone (Intermediate Carbon Content): Located beneath the surface zone, this area has a decreasing carbon concentration. The microstructure here may include a mix of martensite, pearlite, and possibly some retained austenite. The hardness and wear resistance are lower compared to the surface zone, but still significant.
Core Zone (Low Carbon Content): This is the inner part of the cemented layer, where the carbon concentration is the lowest. It is primarily composed of ferrite or a mixture of ferrite and pearlite. This zone remains relatively soft and ductile, providing toughness and absorbing impact while the surface zone handles wear and abrasion.
This gradient in carbon content allows for a balance between a hard, wear-resistant surface and a tougher, more ductile core, enhancing the overall performance and durability of the component.
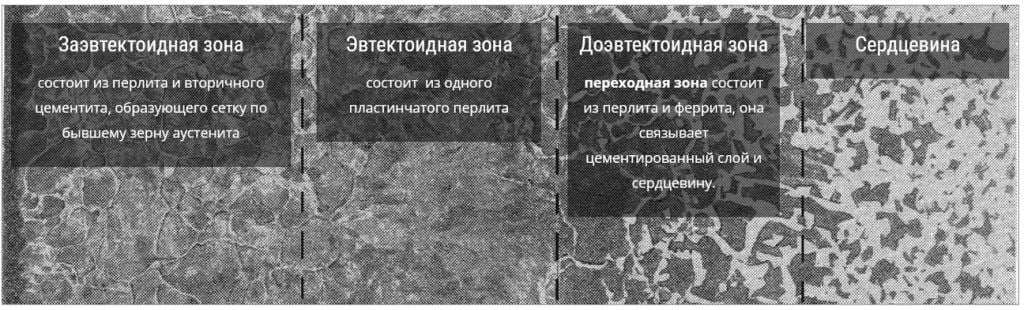
General appearance of the cemented layer on a part made from steel 18XGT
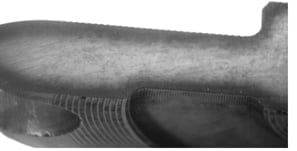
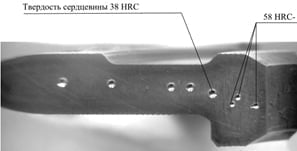

OUR TECHNICAL CAPABILITIES
At our enterprise, cementation is carried out in solid and gaseous carbon-containing environments
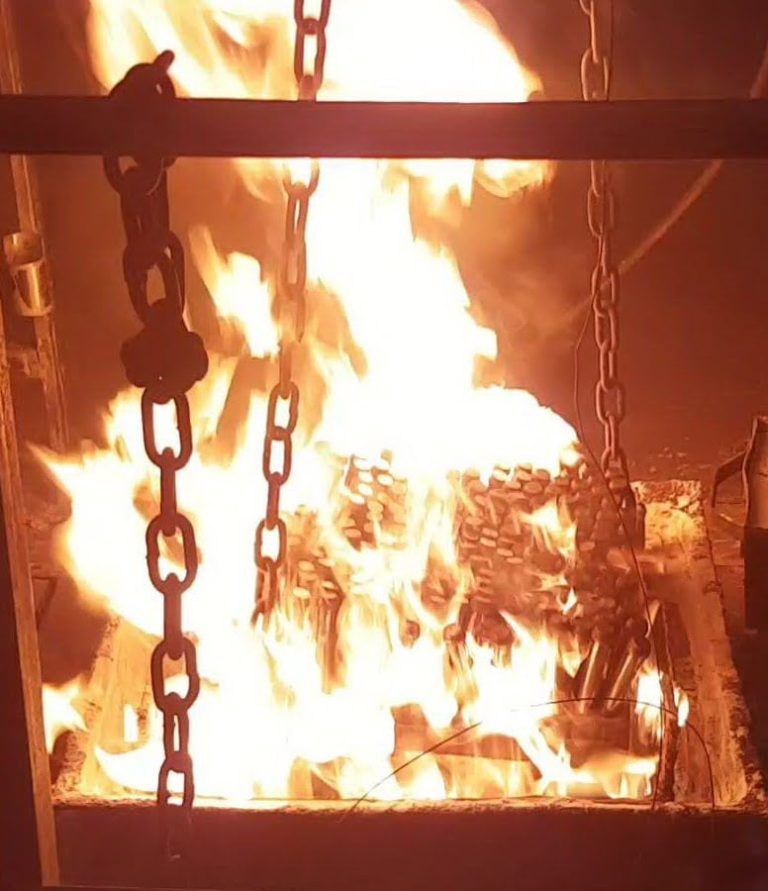
Cementation in a gas environment
Part diameter up to 550 mm
Part length up to 800 mm
Weight up to 150 kg
Hardening of parts after carburization:
- in water up to 200 kg
- in oil up to 100 kg
Gas carburizing is a newer process in which parts are loaded into a furnace into which carburizing gases (carbon monoxide and methane) or liquids are fed, which decompose at high temperatures to form a carburizing atmosphere.
The duration of the gas carburizing process is shorter than that of solid carburizing, since heating and cooling are carried out at higher rates than can be achieved in carburizing boxes. In addition, gas carburizing has a number of other advantages: the ability to precisely regulate the carburizing process by changing the composition of the carburizing gas, the absence of bulky equipment and coal dust, and the ability to quench directly from the furnace.
The gas carburizing process is more economical.
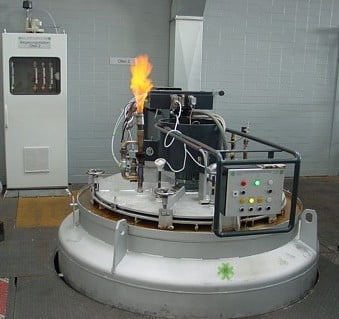
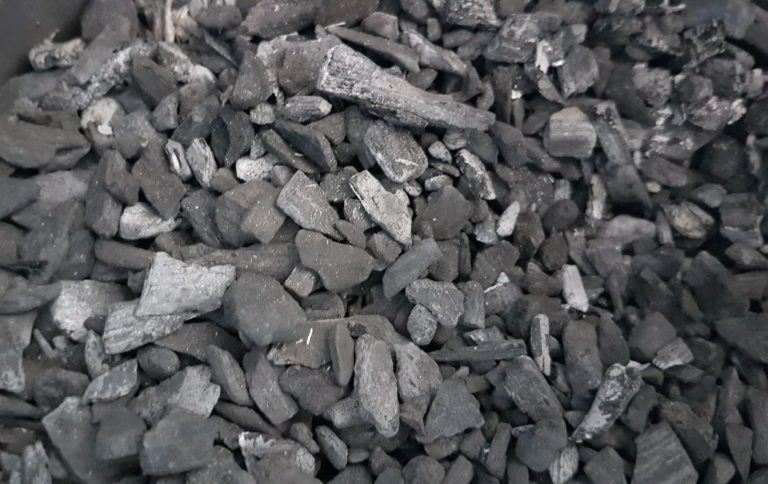
Cementation in solid carburizer
Part diameter up to 600 mm,
Part length up to 1000 mm,
Weight up to 200 kg
The most ancient known method is solid environment cementation.
The parts are placed in a steel box and must be completely covered with carburizer (carbon), without touching each other or the walls of the box.
The box is hermetically sealed and loaded into the furnace.
When heated, carbon monoxide (CO) is formed, which in turn decomposes into carbon dioxide (CO2) and atomic carbon.
Since the parts are heated to a temperature above the critical point Ac3, atomic carbon penetrates into the soft iron.
Processing modes: 900-950 ° C, 1 hour of holding per 0.1 mm of the thickness of the cemented layer. To obtain a 1 mm layer – holding for 10 hours.
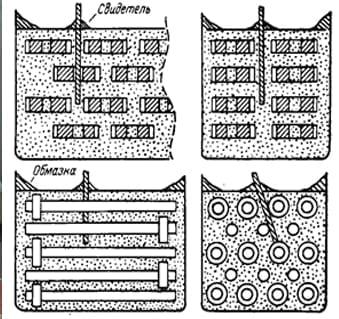
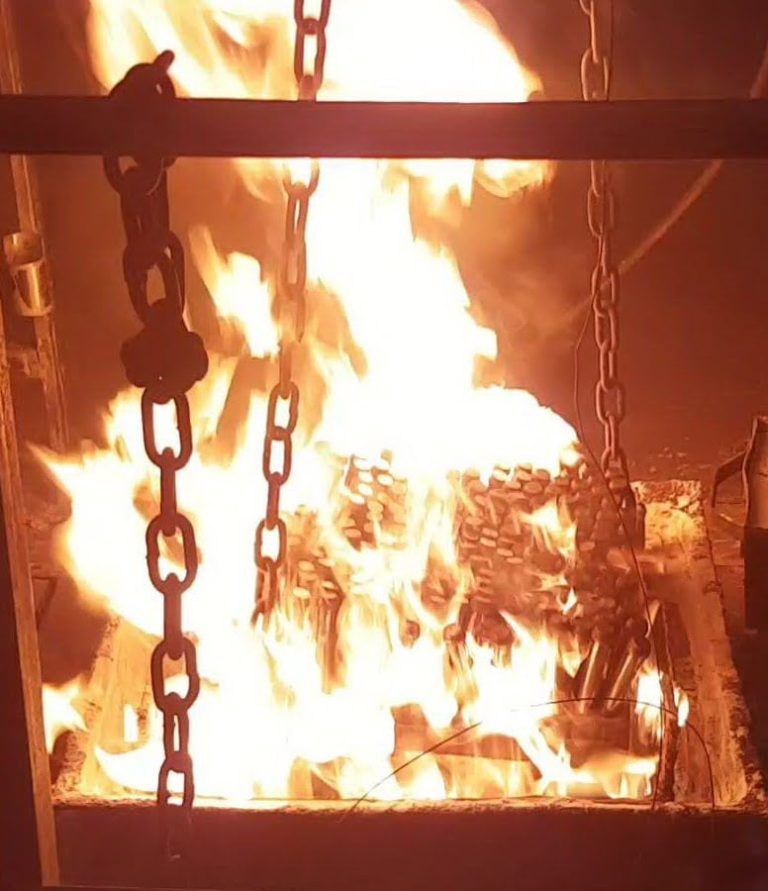
Cementation in a gas environment
Part diameter up to 550 mm
Part length up to 800 mm
Weight up to 150 kg
Hardening of parts after carburization:
- in water up to 200 kg
- in oil up to 100 kg
Gas carburizing is a newer process in which parts are loaded into a furnace into which carburizing gases (carbon monoxide and methane) or liquids are fed, which decompose at high temperatures to form a carburizing atmosphere.
The duration of the gas carburizing process is shorter than that of solid carburizing, since heating and cooling are carried out at higher rates than can be achieved in carburizing boxes. In addition, gas carburizing has a number of other advantages: the ability to precisely regulate the carburizing process by changing the composition of the carburizing gas, the absence of bulky equipment and coal dust, and the ability to quench directly from the furnace.
The gas carburizing process is more economical.
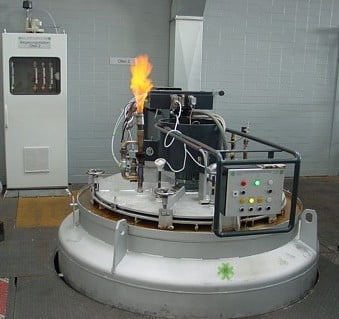
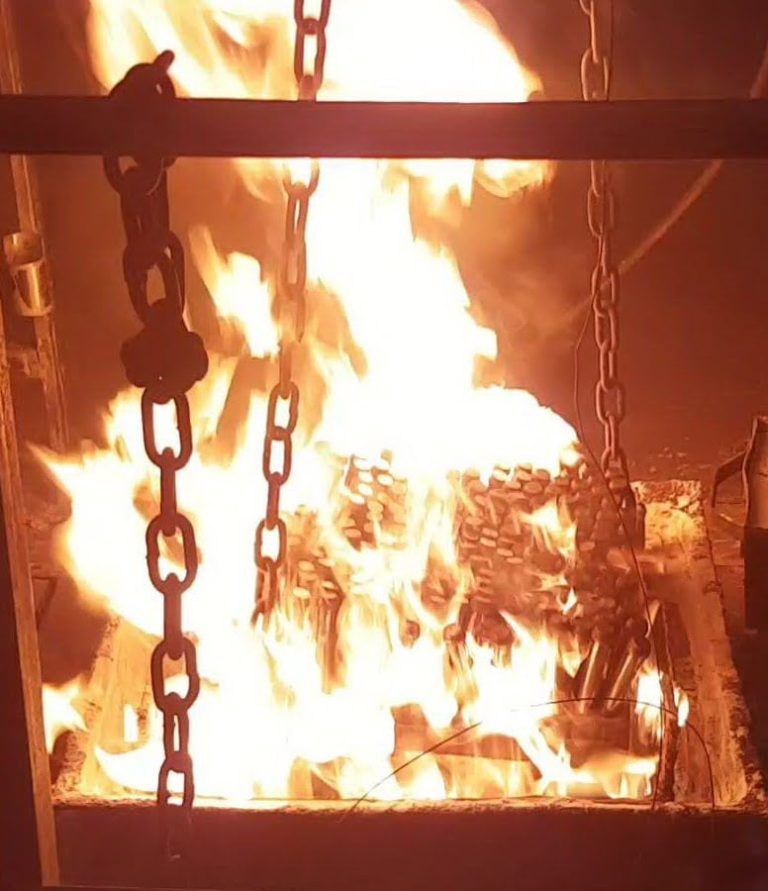
Cementation in solid carburizer
Part diameter up to 600 mm,
Part length up to 1000 mm,
Weight up to 200 kg
The most ancient known method is solid environment cementation.
The parts are placed in a steel box and must be completely covered with carburizer (carbon), without touching each other or the walls of the box.
The box is hermetically sealed and loaded into the furnace.
When heated, carbon monoxide (CO) is formed, which in turn decomposes into carbon dioxide (CO2) and atomic carbon.
Since the parts are heated to a temperature above the critical point Ac3, atomic carbon penetrates into the soft iron.
Processing modes: 900-950 ° C, 1 hour of holding per 0.1 mm of the thickness of the cemented layer. To obtain a 1 mm layer – holding for 10 hours.
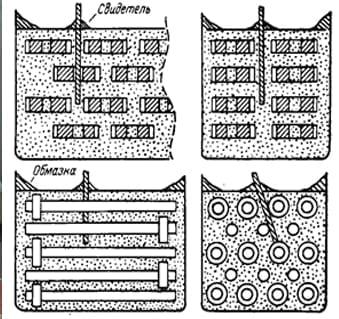

WHAT MATERIALS ARE SUBJECT TO CEMENTATION

PROPERTIES OF STEEL AFTER CEMENTATION
As a result of carburization, only favorable distribution of carbon over the section is achieved. The final properties of the carburized part are formed by subsequent heat treatment.
All products are subjected to hardening with low tempering. After hardening, the carburized product acquires high hardness (50-58HRC) and wear resistance, the limit of contact endurance and the limit of endurance in bending increase, while maintaining a viscous core.
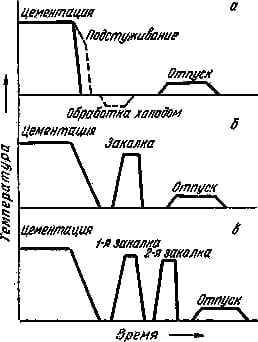
Hardness of the surface and core of 18XGT steel parts after cementation, quenching, and low tempering
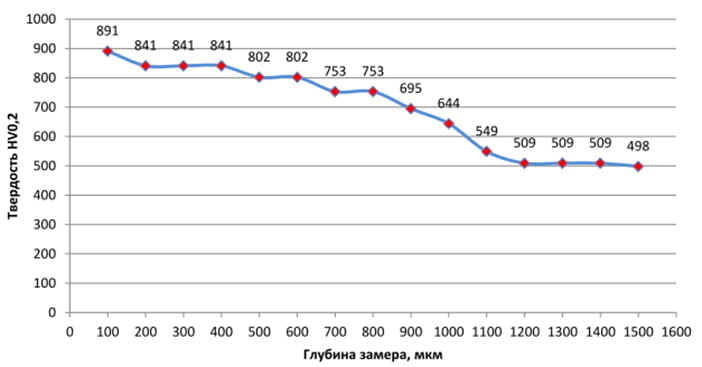
Cementation is a chemical-thermal treatment that involves the diffusion of carbon atoms into the surface layer of steel products by heating to a temperature of 900-950 °C.
Cementation is applied to low-carbon steel (up to 0.25%) or low-alloyed low-carbon steels such as: 20G, 20H, 20HF, 12HNZA, 20X2N4A, 18XGT, 18X2N4VA, 20XGNR, and others.
This treatment is applied to machine and apparatus parts that must have a wear-resistant working surface and a tough core. For example: gear wheels, crankshafts, cam followers, worms, piston pins, plow shares, and others.
Distribution of microhardness in the cemented layer of 18XGT steel after 10 hours of cementation, quenching, and low tempering
The cementation process can significantly increase hardness and strength, enhance wear resistance and corrosion resistance.
Cementation of steel is a complex chemical-thermal treatment at a temperature of 900-950 degrees Celsius resulting in the saturation of steel with carbon atoms. Cementation of steel 40X, 45 steel, 20X steel, 18XGT steel is possible in gaseous and solid carbon-containing media. This procedure is applied to parts of mechanisms that must have a tough core and a wear-resistant surface, for example, plowshares, crankshafts, piston pins, gear wheels.
Types of Cementation
Gas cementation of stainless steel takes place in specially equipped furnaces where cementing gases are introduced. The gas cementation process is very economical and faster than cementation in a solid medium.
Cementation of steel using carburizer (coal) is called cementation in a solid medium. During this process, carbon oxide is formed upon heating from which atomic carbon diffuses into the metal. To achieve a cemented layer of 1 mm, 10 hours of exposure at temperatures above nine hundred degrees is required.
Our company “Karbaz” performs cementation of steel in salts, gases, and solid media using the most modern equipment. Cementation in a carburizer involves loading 200 kg of parts with a diameter of up to 600 mm and a length of up to 1000 mm. Cementation in a gas medium is possible for 150 kg of steel products with a diameter of 550 mm and a length of up to 800 mm. After cementation, the parts are quenched in water or oil.
The cementation service is popular in Ukraine, and our prices are very reasonable and democratic. To order cementation, call the manager or leave a request on the website.
Cementation – of drums, gears, pulleys, and much more.
Karbaz provides cementation services for steel, metal 40X, 45X, 20X, 18XGT, and stainless steel in molten salts. This is a surface hardening process by enriching the metal with carbon in its surface layer.
Advantages of cementation in molten salts include higher wear and corrosion resistance, as well as greater hardness and wear resistance compared to other hardening methods.
Karbaz uses a special salt mixture that allows achieving the desired thickness of the surface layer and specific metal characteristics. After cementation, we perform annealing to achieve the desired metal structure and properties.
Cementation is an important process for many industries, including automotive manufacturing, mechanical processing, and tool production. Karbaz can handle both individual parts and large batches according to customer requirements.
When contacting Karbaz, you can be assured of high-quality service and precise achievement of the required metal characteristics. Our experienced staff ensures that each part undergoes a strict quality control process to guarantee the best results. Contact us to find out how we can assist you in your production.